In addition to the temperature, factors such as the heat sealing time, heat sealing pressure, packaging materials, and equipment maintenance can also affect the heat sealing effect of the flat double-chamber vacuum packaging machine. The following is a detailed introduction:
Heat Sealing Time
If the heat sealing time is too short, the hot melt adhesive layer of the packaging material cannot be fully melted, resulting in an insecure seal. On the other hand, if the heat sealing time is too long, it will not only reduce work efficiency but may also cause the packaging material to overheat, leading to problems such as embrittlement and deformation at the seal. Different packaging materials and heat sealing temperatures require corresponding heat sealing times, which generally range from 2 to 5 seconds and need to be adjusted according to the actual situation.
Heat Sealing Pressure
An appropriate heat sealing pressure can make the packaging materials closely fit during heat sealing, ensuring that the molecules at the seal fully merge and form a good seal. If the heat sealing pressure is insufficient, there will be gaps at the seal, causing air leakage. Excessive pressure may squeeze and deform the packaging material, or even damage the product, and it will also accelerate the wear of the heat sealing components. Usually, the heat sealing pressure needs to be adjusted according to the thickness and material of the packaging material. For thin plastic films, the heat sealing pressure is generally 0.2 - 0.3MPa; for thicker composite materials, the pressure may need to be adjusted to 0.3 - 0.5MPa.
Packaging Materials
- Material: The heat sealing performance of different packaging materials varies greatly. For example, polyethylene (PE) film has good heat sealing performance and a relatively wide heat sealing temperature range. In contrast, polyester (PET) film requires a higher heat sealing temperature and is more sensitive to heat sealing conditions. In addition, multi-layer composite packaging materials are more difficult to heat seal due to the different materials of each layer, and more precise control of heat sealing parameters is required.
- Thickness: The thickness of the packaging material directly affects the heat sealing effect. Thicker materials require higher temperatures, longer times, and greater pressure to achieve a good heat seal, while thinner materials are easily damaged by overheating or excessive pressure.
- Surface Treatment: The surface treatment method of the packaging material also affects the heat sealing effect. For example, the surface energy of the film treated by corona treatment is increased, which is conducive to the adhesion of the materials during heat sealing. However, packaging materials with oil stains, dust, or moisture on the surface will hinder the fusion of the materials during heat sealing, resulting in an insecure seal.
Equipment Maintenance
- Cleaning of Heat Sealing Components: After long-term use, impurities such as debris of packaging materials and glue will remain on the surface of heat sealing strips and hot pressing frames and other components. These impurities will affect the heat sealing effect, resulting in uneven or insecure seals. Therefore, it is necessary to regularly wipe the heat sealing components with a clean cloth, and use a special cleaning agent for cleaning when necessary.
- Wear of Heat Sealing Components: Heat sealing strips and hot pressing frames will gradually wear out during frequent heat sealing processes. Worn components cannot provide uniform heat sealing pressure and temperature, thus affecting the heat sealing effect. When it is found that the heat sealing components are severely worn, they should be replaced in a timely manner.
- Electrical System of the Equipment: The electrical system of the equipment controls parameters such as heat sealing temperature and time. If electrical components malfunction, such as a malfunctioning temperature sensor or a damaged relay, it will lead to inaccurate heat sealing parameters and affect the heat sealing effect. Therefore, it is necessary to regularly inspect and maintain the electrical system of the equipment to ensure its normal operation
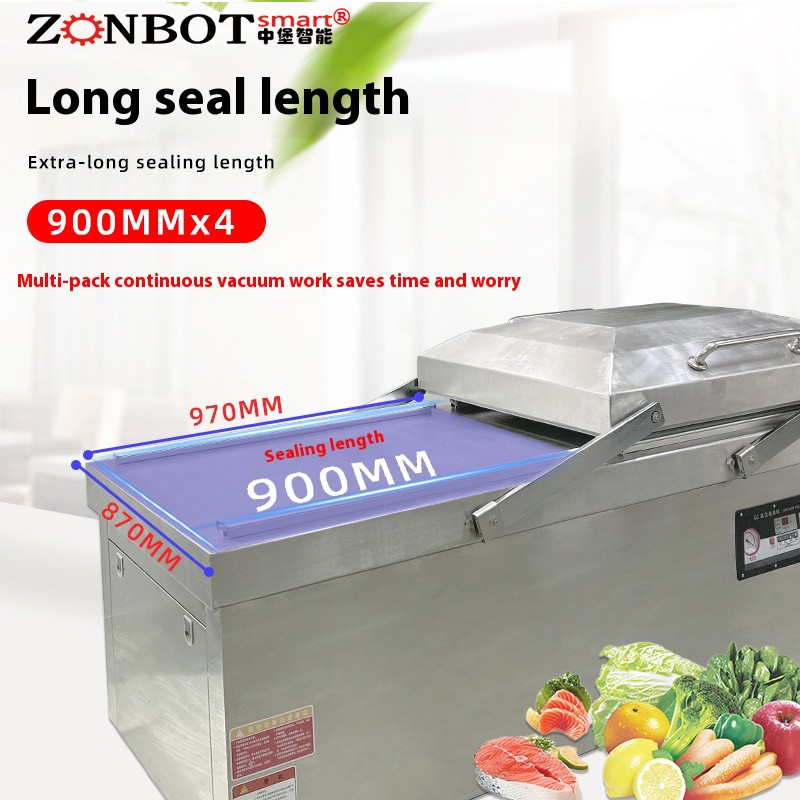
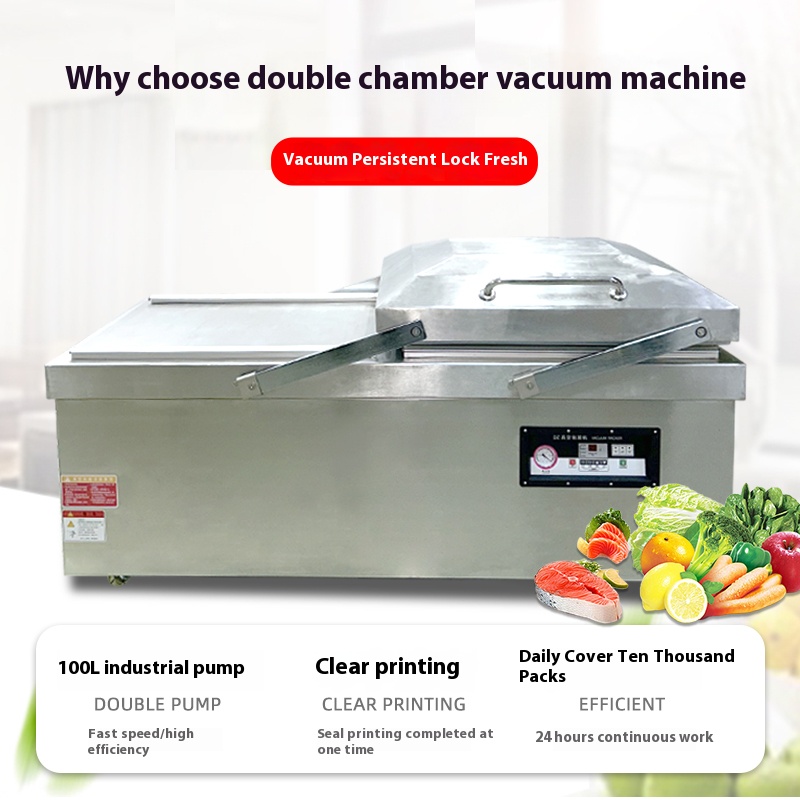
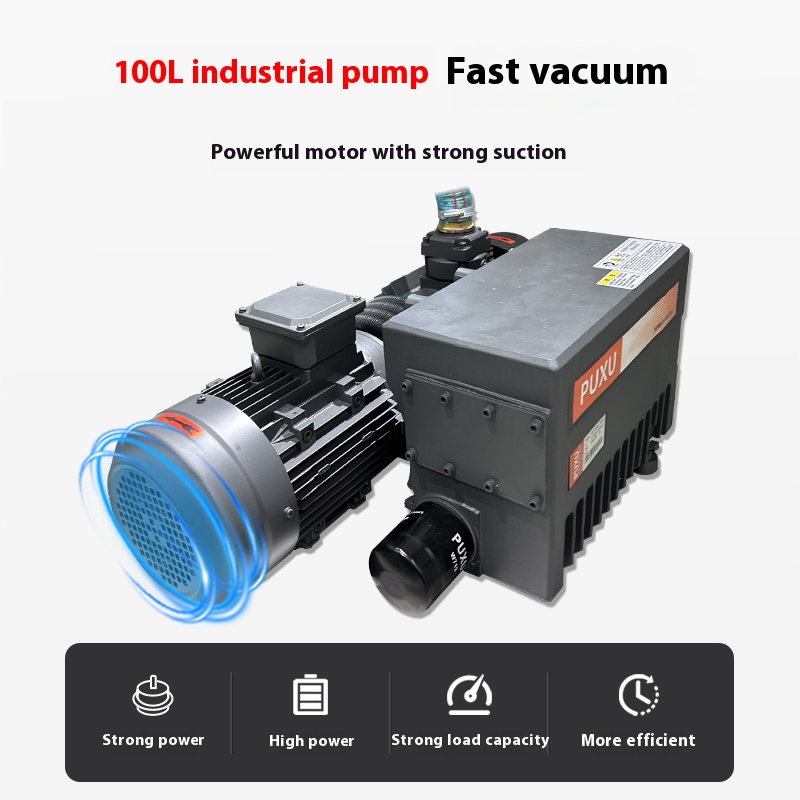
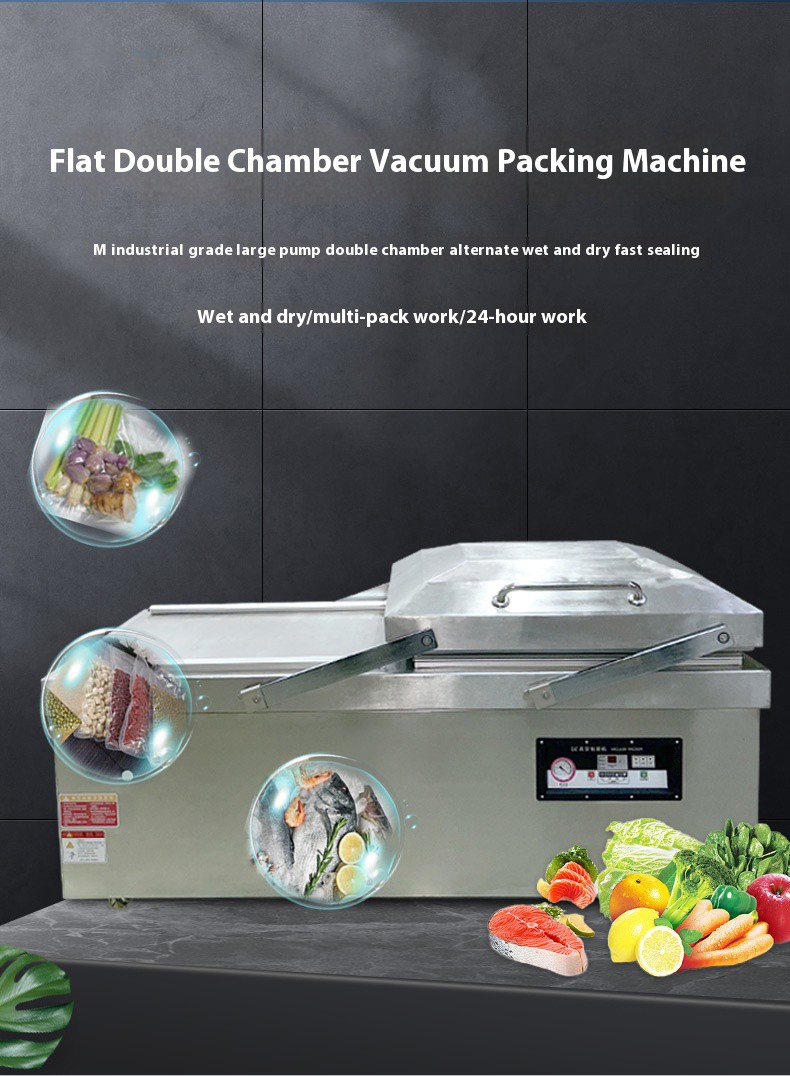
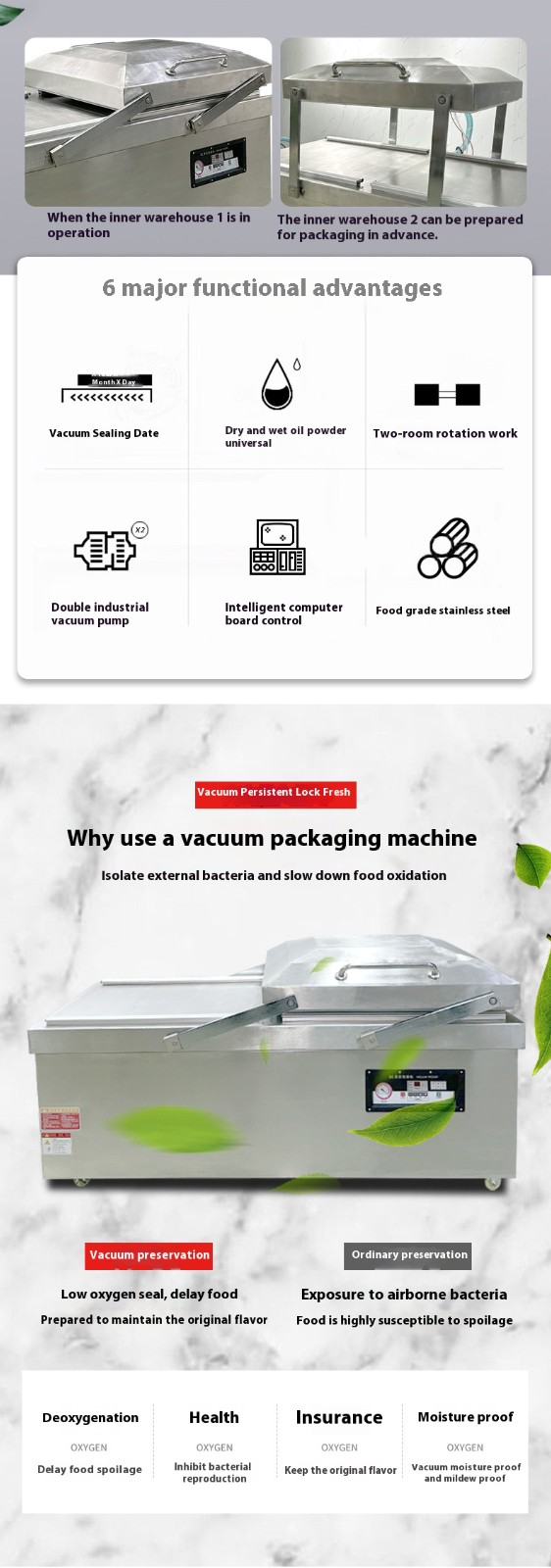
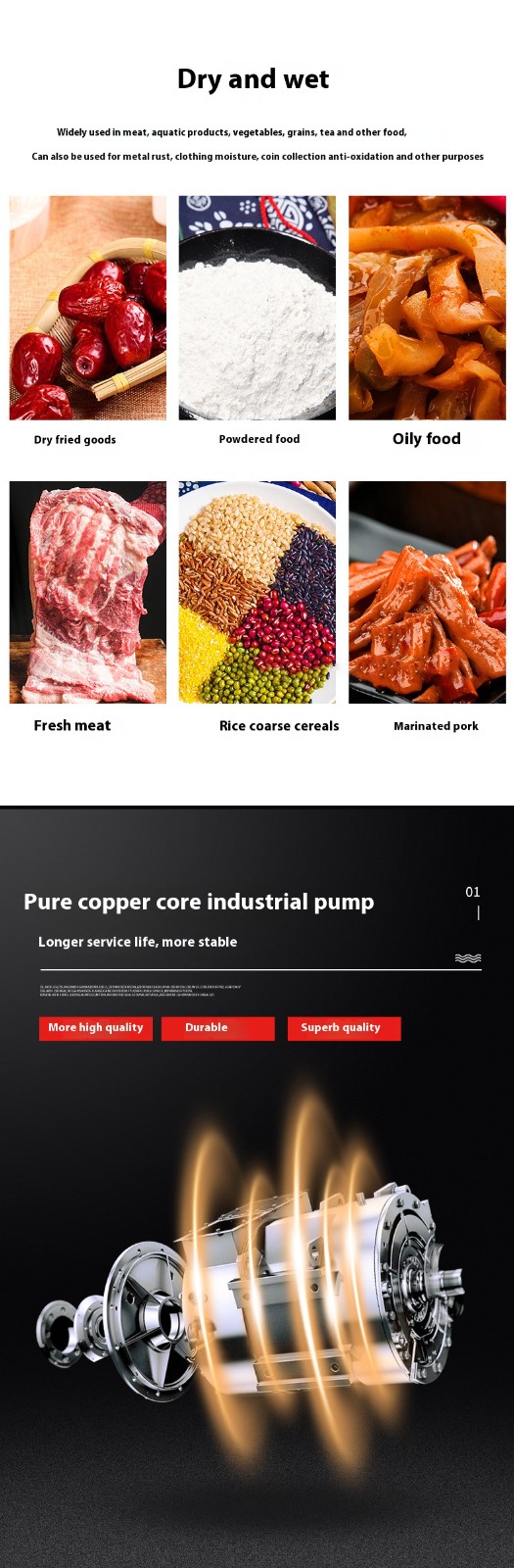
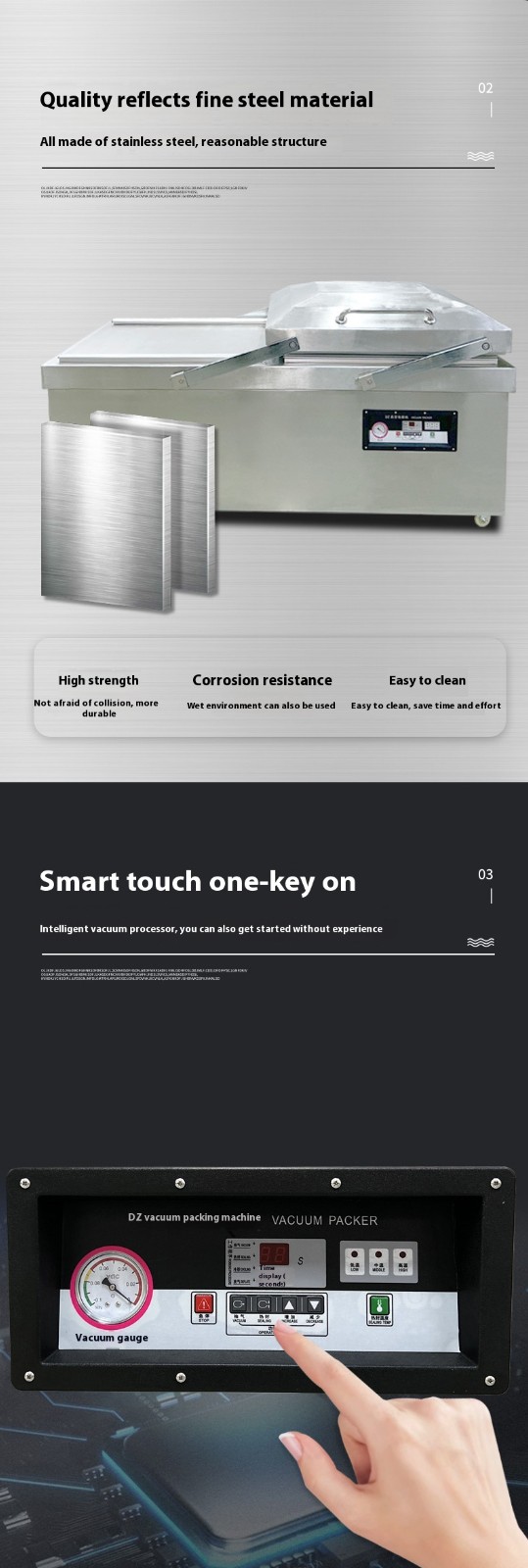
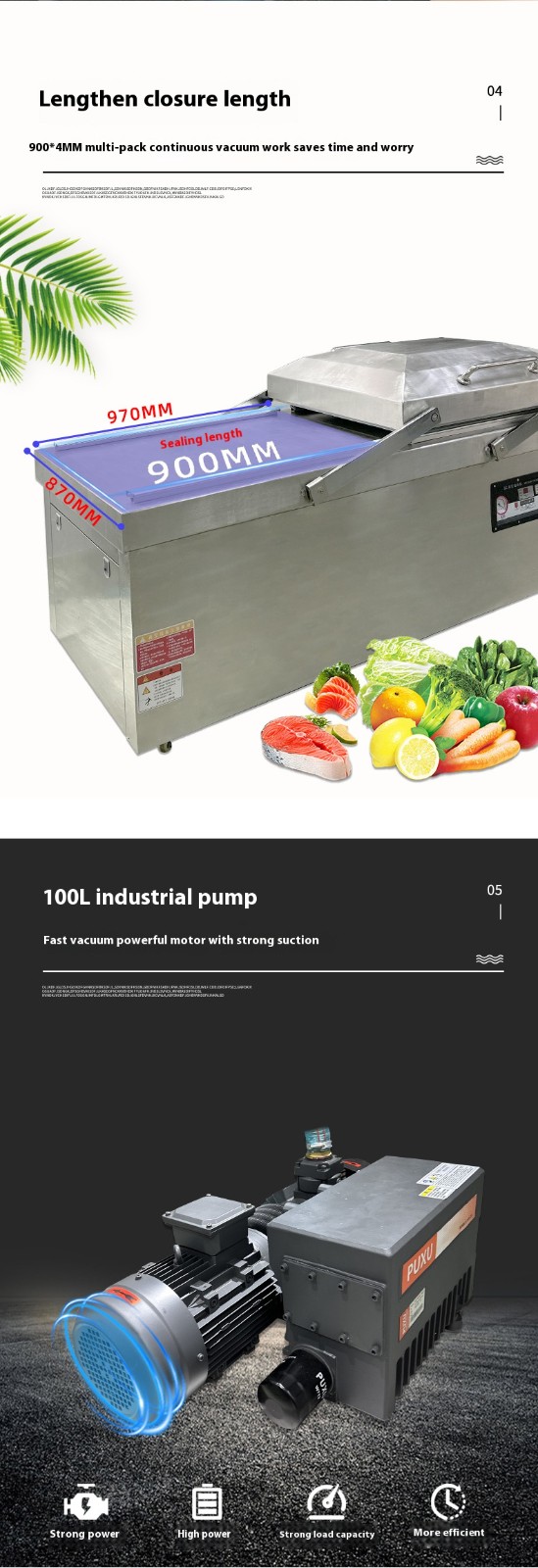
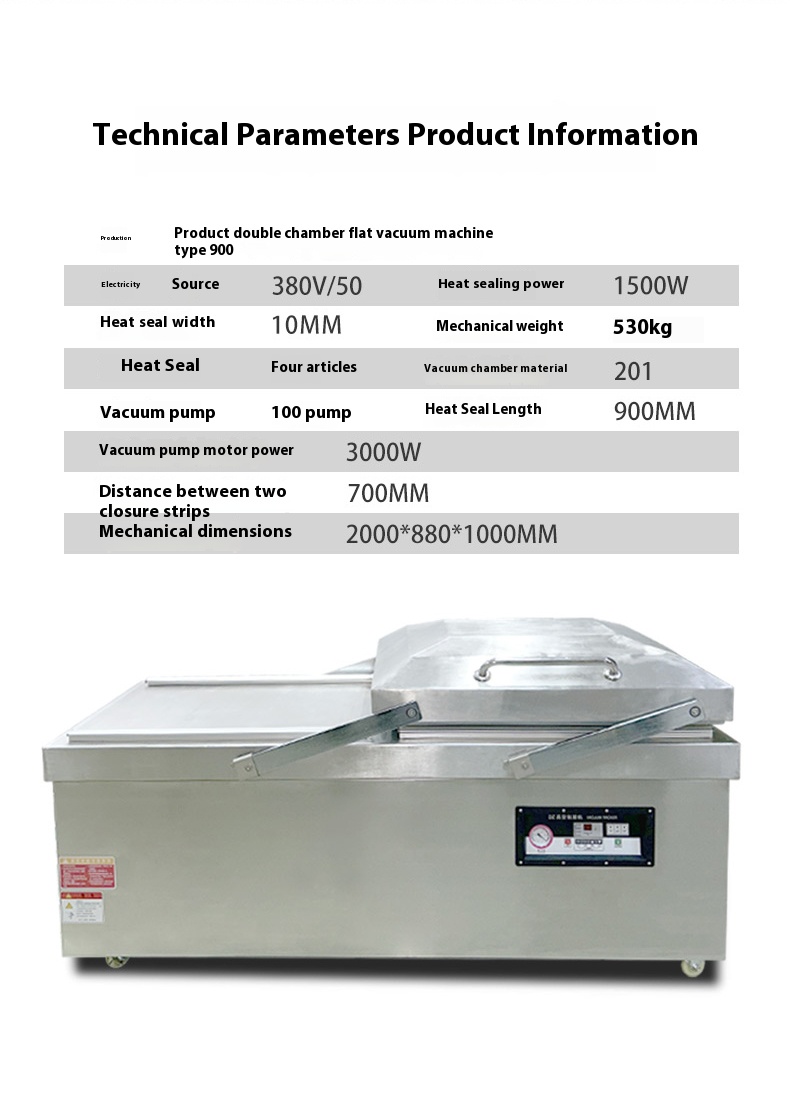
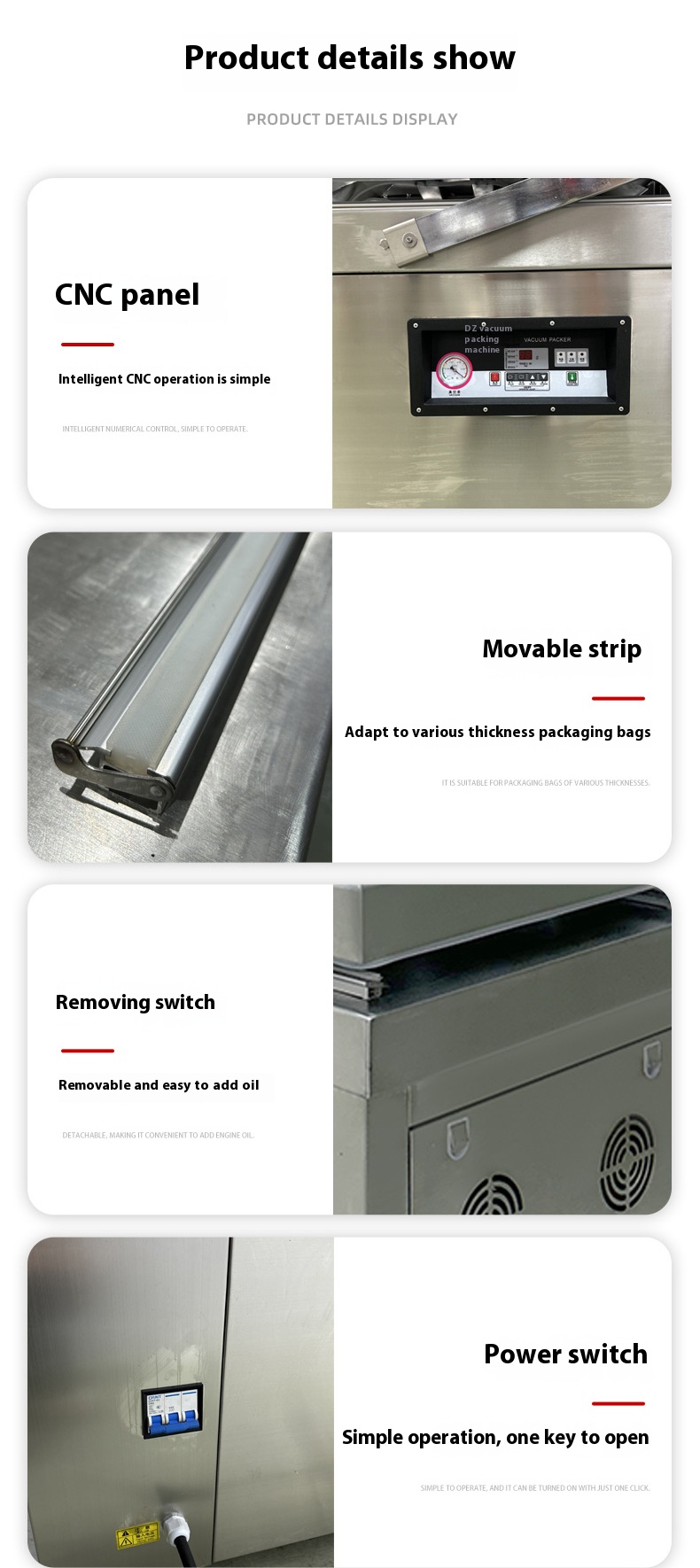
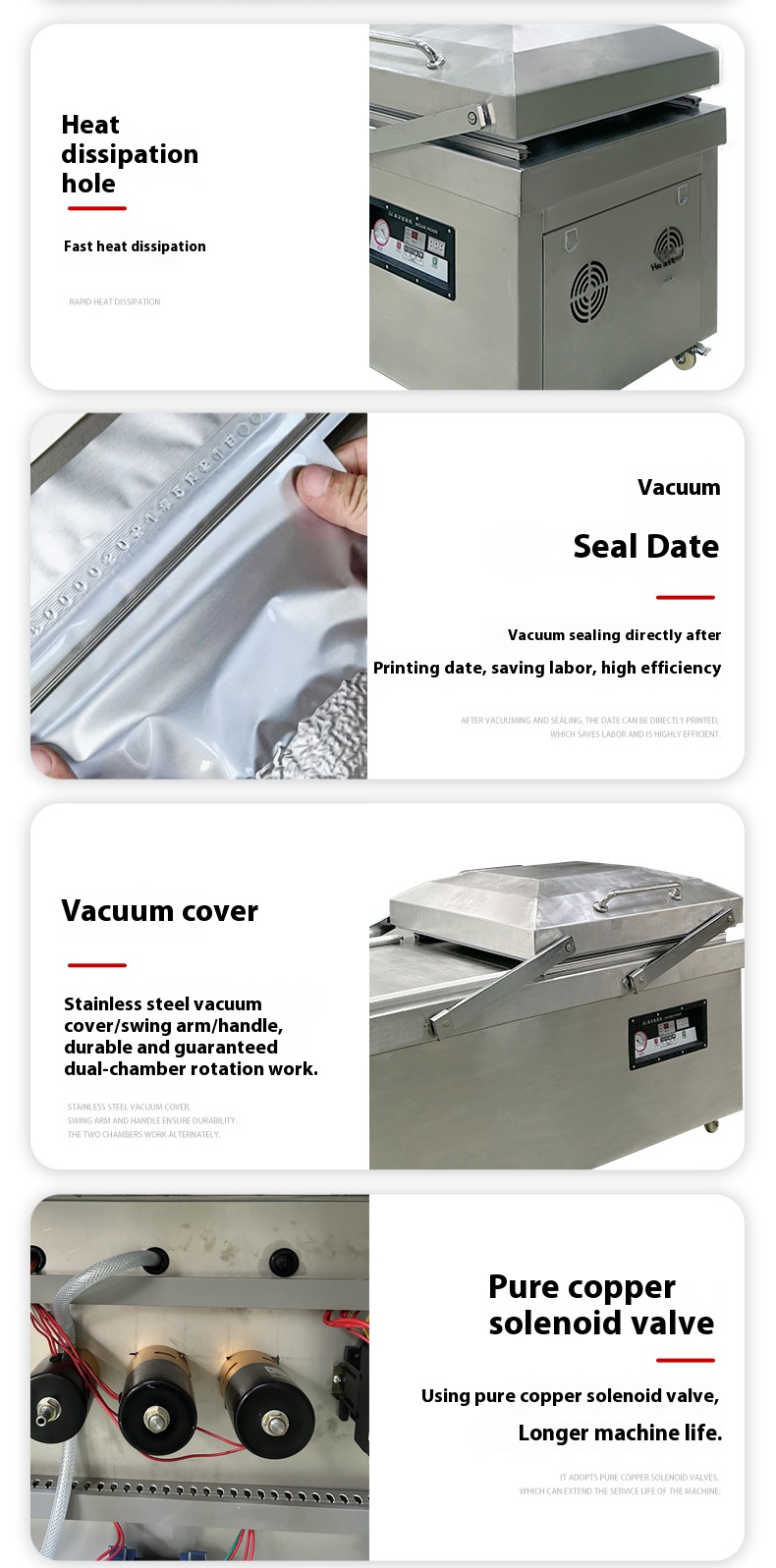
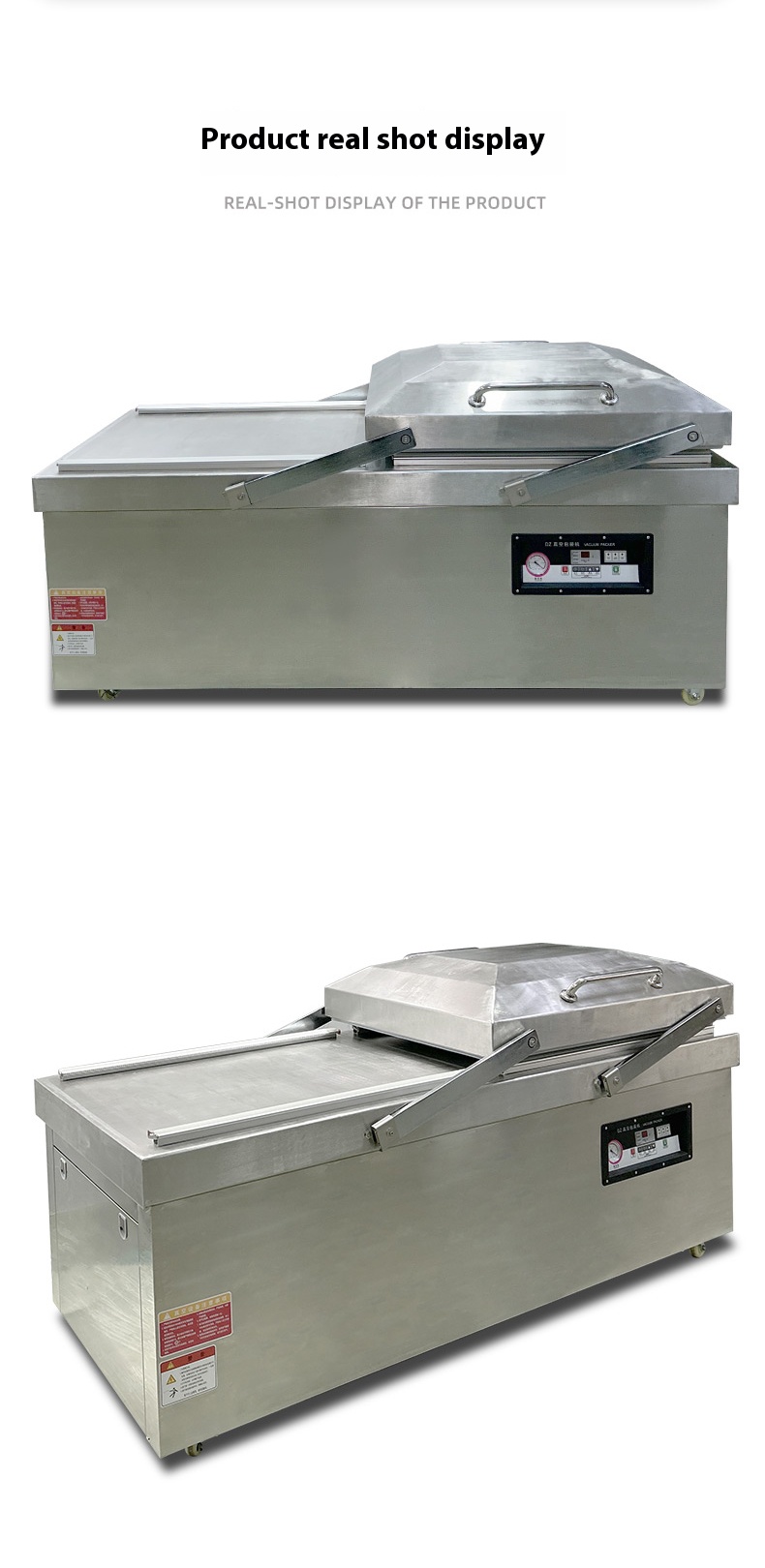