Here is the English version of the flexibility of round bottle positioning labeling machines in different production environments, explained through hardware modular design, parameter adaptive adjustment, multi-scenario function adaptation, etc.:
- Wide range of bottle compatibility: By adjusting the spacing of the bottle separating wheel and the height of the conveyor belt, it can adapt to round bottles with a diameter of 50–200mm and a height of 100–350mm (such as mineral water bottles, canned bottles, and short cosmetic bottles). Some models are equipped with quick-change fixtures, allowing bottle type switching within 15 minutes.
- Flexible adaptation to label specifications: The label tape reel supports label rolls with a diameter of 30–300mm. The servo motor adjusts the label feeding speed to match labels of different materials (such as paper, PVC, PET) and types (such as single labels, double labels, and transparent labels) — for example, large body labels for beverage bottles and small warning labels for pharmaceutical bottles.
- Expandable number of labeling heads: The basic model is equipped with a single labeling head, supporting single-position labeling (such as neck labels or body labels). For multi-position labeling (such as front + back labels), dual labeling heads or rotating trays can be added to achieve simultaneous attachment (e.g., one-time packaging of multiple labels for wine bottles).
- Flexible integration of coding modules: Thermal coding, inkjet coding, or laser coding modules can be added as needed. The coding position can be set before, during, or after labeling — for example, food industries print production dates after labeling, while pharmaceutical industries code first and then label to cover partial information.
- Low-speed mode (50–100 bottles/minute): Suitable for small-batch trial production and labeling of special-shaped bottles (such as handmade essential oil bottles), facilitating manual quality monitoring.
- High-speed mode (150–500 bottles/minute): Adapted to large-scale production lines for beverages and beer, 联动 (linking) with front-end filling equipment and back-end cartoning machines for flexible capacity matching.
- Through the touchscreen, the circumferential angle (e.g., aligning the label with the logo) and axial height (e.g., middle of the bottle body or neck) of the label on the bottle can be set, supporting ±180° rotational positioning and 0–300mm height adjustment. This meets different packaging design needs — for example, avoiding the pump head when labeling shampoo or emptying the sealing position for cans.
- Moisture-resistant design: The conveyor chain plate and labeling head are made of 316L stainless steel, resistant to cleaning and disinfection (such as CIP in-situ cleaning for beverage production lines), preventing labels from falling off due to moisture.
- Elastic capacity matching: In peak seasons, enable high-speed labeling mode (e.g., 500 bottles/minute for mineral water lines); in off-seasons, switch to small-batch, multi-variety production (e.g., only 30 minutes for juice beverage model changeover).
- Visual positioning + traceability function: Visual cameras identify scale lines on bottles to ensure labels align with drug instruction texts (accuracy ±0.2mm). Meanwhile, integrate QR code coding modules to meet drug regulatory code traceability requirements — for example, printing the unique code of each medicine bottle at the specified label position.
- Aseptic environment adaptation: The equipment surface is polished with a dead-angle-free design, complying with GMP standards. It can be connected to the control system of a clean workshop to 联动 (link) with sterilization equipment.
- Synchronous multi-position labeling: Supports one-time attachment of neck labels (brand logos), body labels (ingredient instructions), and back labels (usage guides). Multiple groups of sensors ensure uniform label spacing — for example, three-label linkage labeling for shampoo.
- Flexible material adaptation: For hose-type round bottles (such as hand cream), flexible label covering belts are used to avoid extrusion deformation. Meanwhile, visual systems monitor the flatness of transparent labels in real-time to detect bubbles.
- For e-commerce customized products (such as small-batch customized label wines), production parameters (such as label content and position) can be called with one click through stored production recipes, completing changeover within 10 minutes to reduce downtime costs. This adapts to the "multi-variety, small-batch" production model.
- The system can store over 100 production recipes (such as bottle types, label specifications, and coding contents for different products). When changing products, simply call the recipe without re 调试 (recommissioning), suitable for factories with multi-variety rotation production (e.g., daily chemical enterprises producing shampoo, body wash, etc., simultaneously).
- Connect to the factory MES system via protocols like OPC UA and Modbus, automatically adjusting labeling parameters based on order data (e.g., printing specific batch numbers as required by orders). Or link with front-end weighing equipment to label only qualified products — for example, labeling after weight sorting in the food industry.
- High/low-temperature environments: In cold storage (such as cold drink production lines) or high-temperature workshops (such as direct labeling after can sterilization), the equipment uses temperature-resistant motors and sensors to ensure stable operation at -10°C–60°C.
- Explosion-proof scenarios: For the chemical industry (such as alcohol products), explosion-proof servo motors and electrical systems can be optionally configured to meet explosion-proof certification requirements (such as ATEX and IECEx), avoiding spark risks.
Through the design of "hardware modularization + parameter intelligence + scenario customization", round bottle positioning labeling machines can quickly adapt to different industries, production capacities, and product specifications. They not only meet the efficiency needs of large-scale standardized production but also support flexible switching for small-batch customized production — especially suitable for enterprises with multi-variety mixed production to reduce changeover costs and enhance production line flexibility
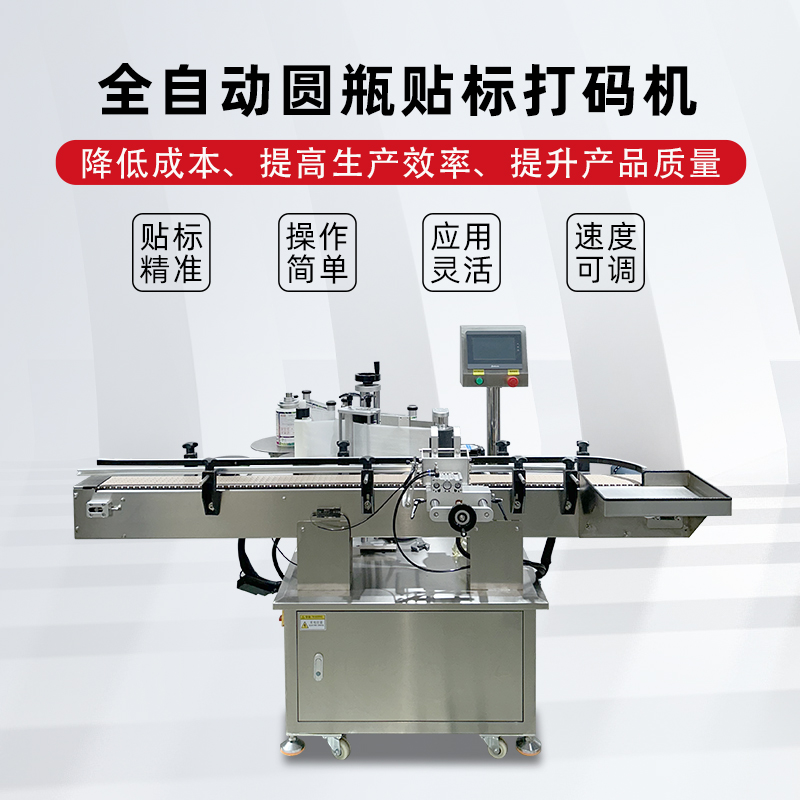
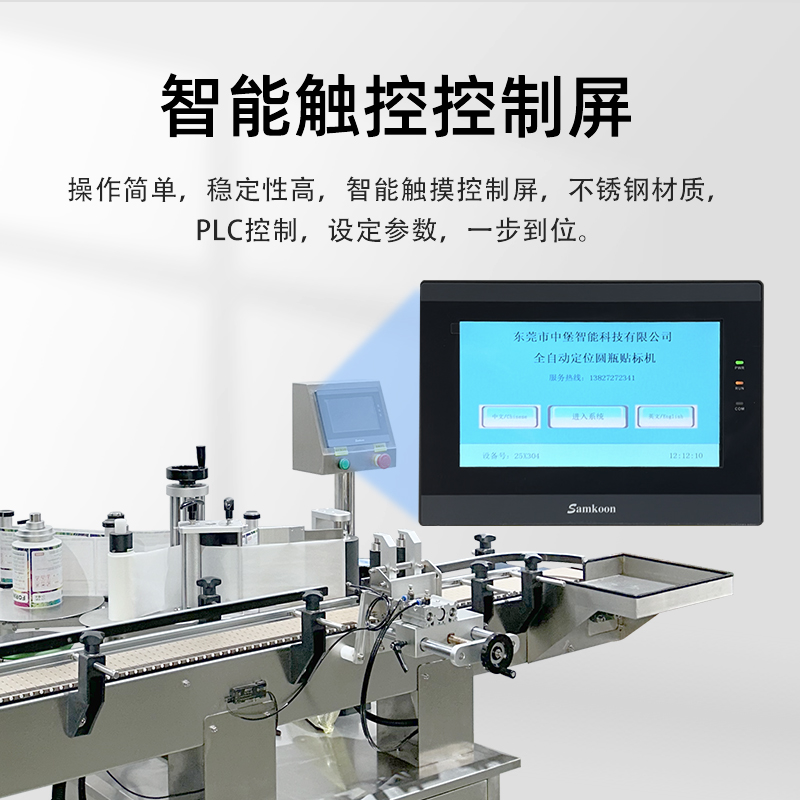
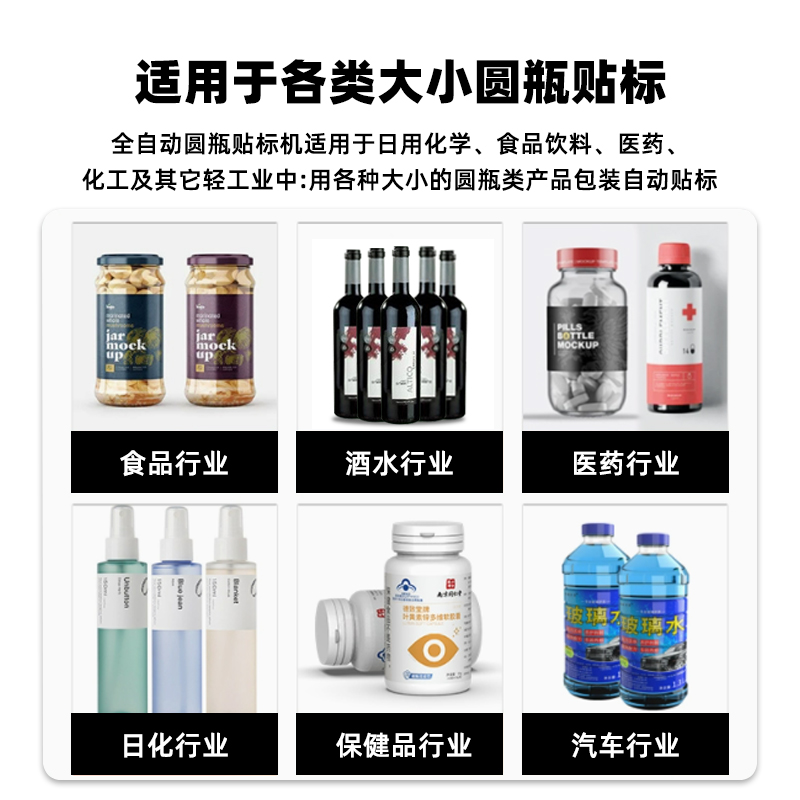
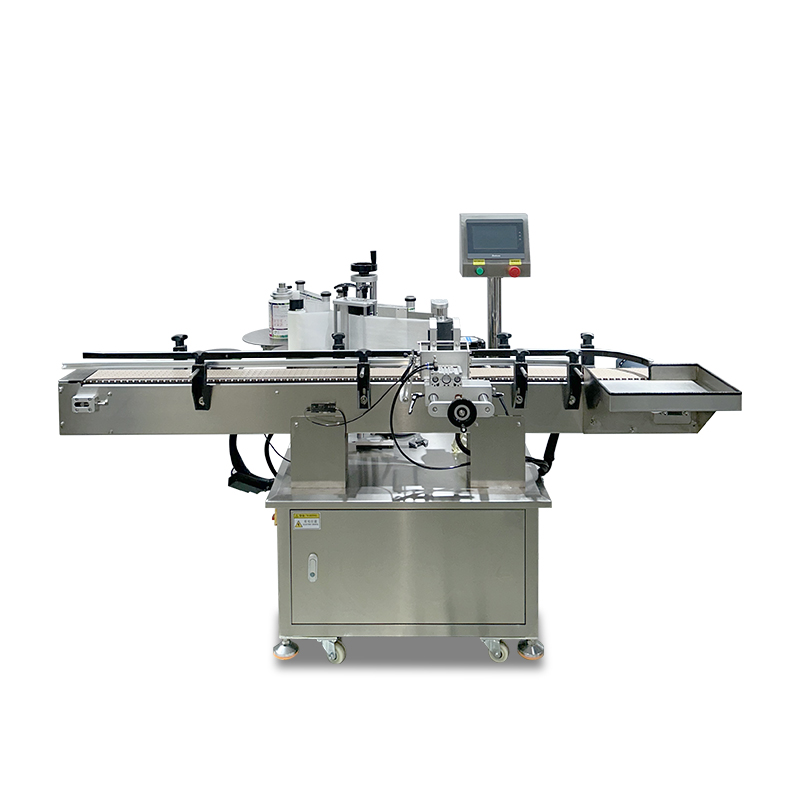
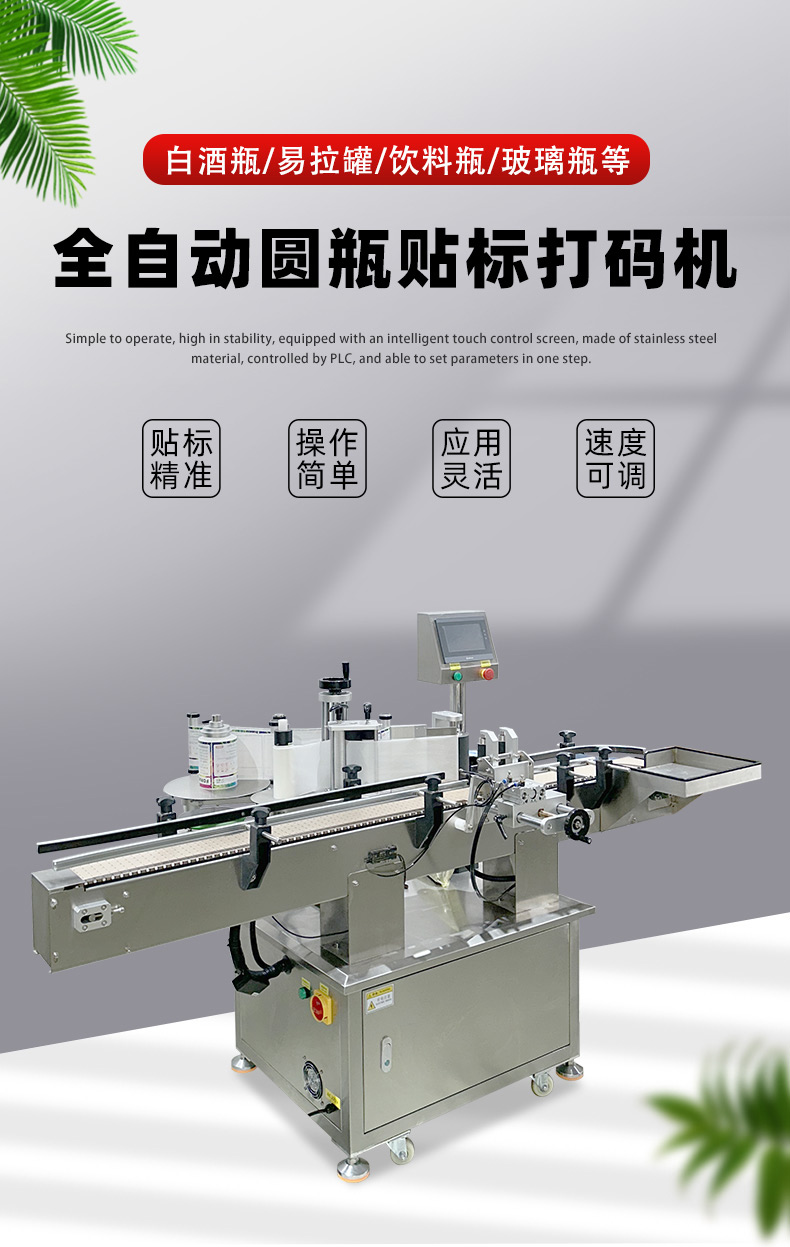
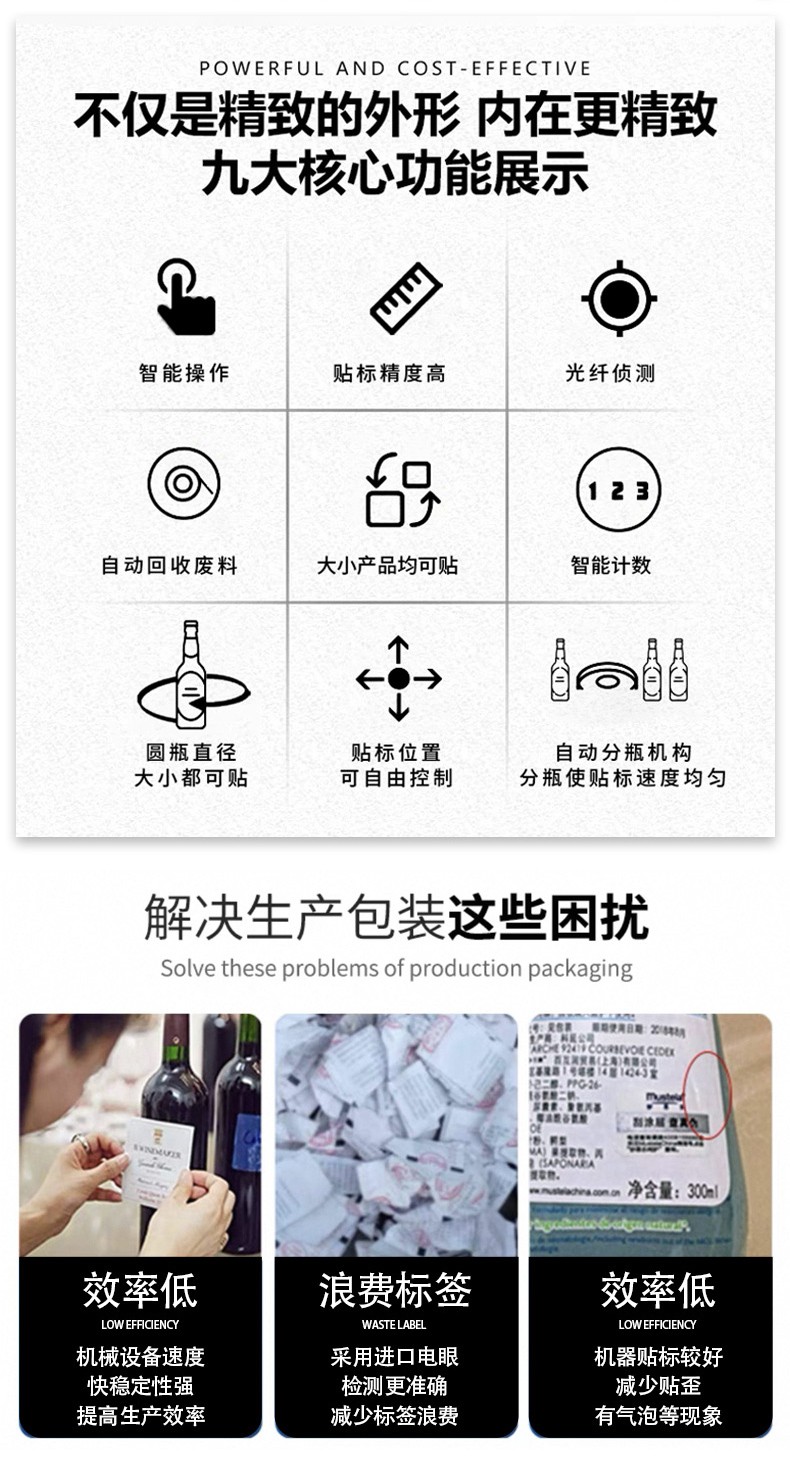
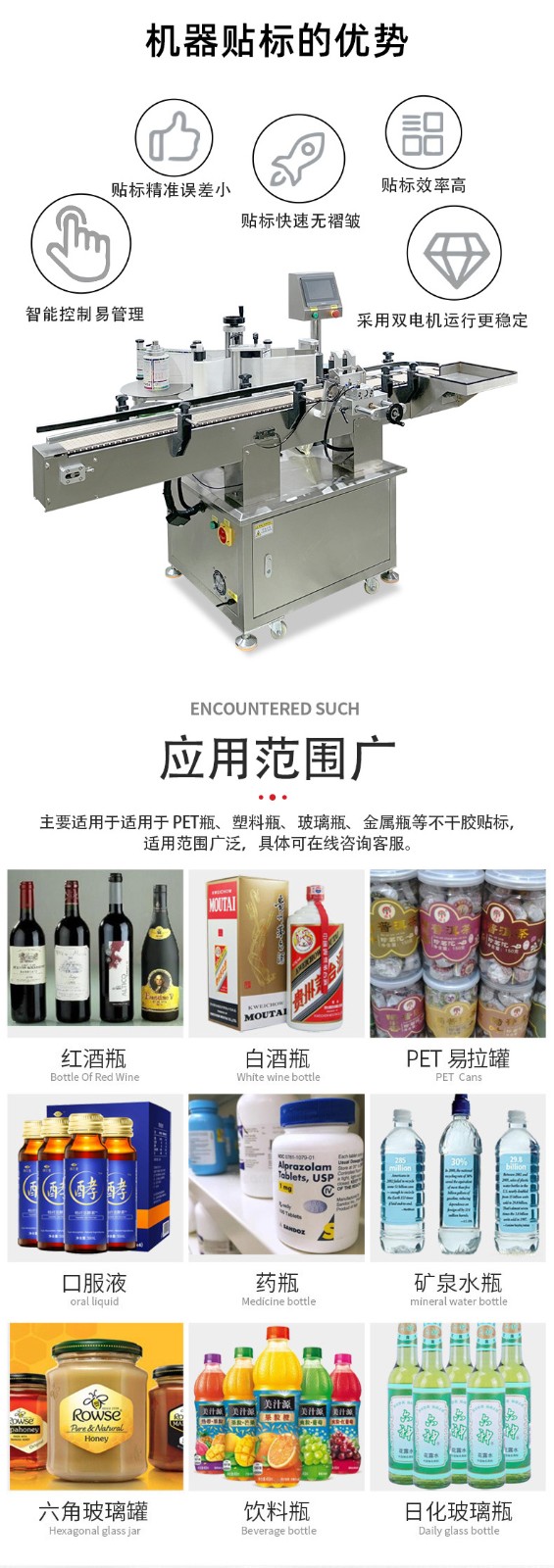
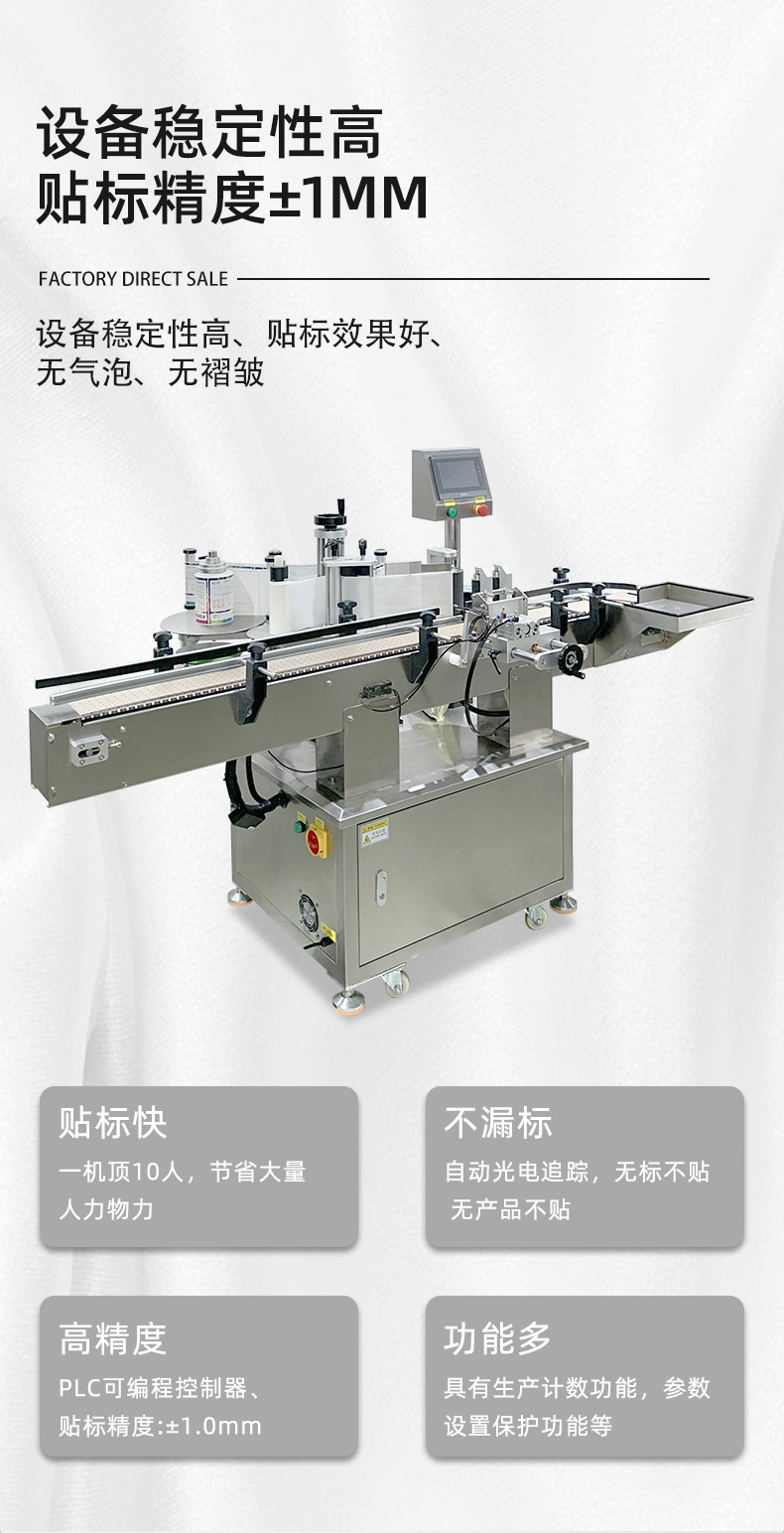
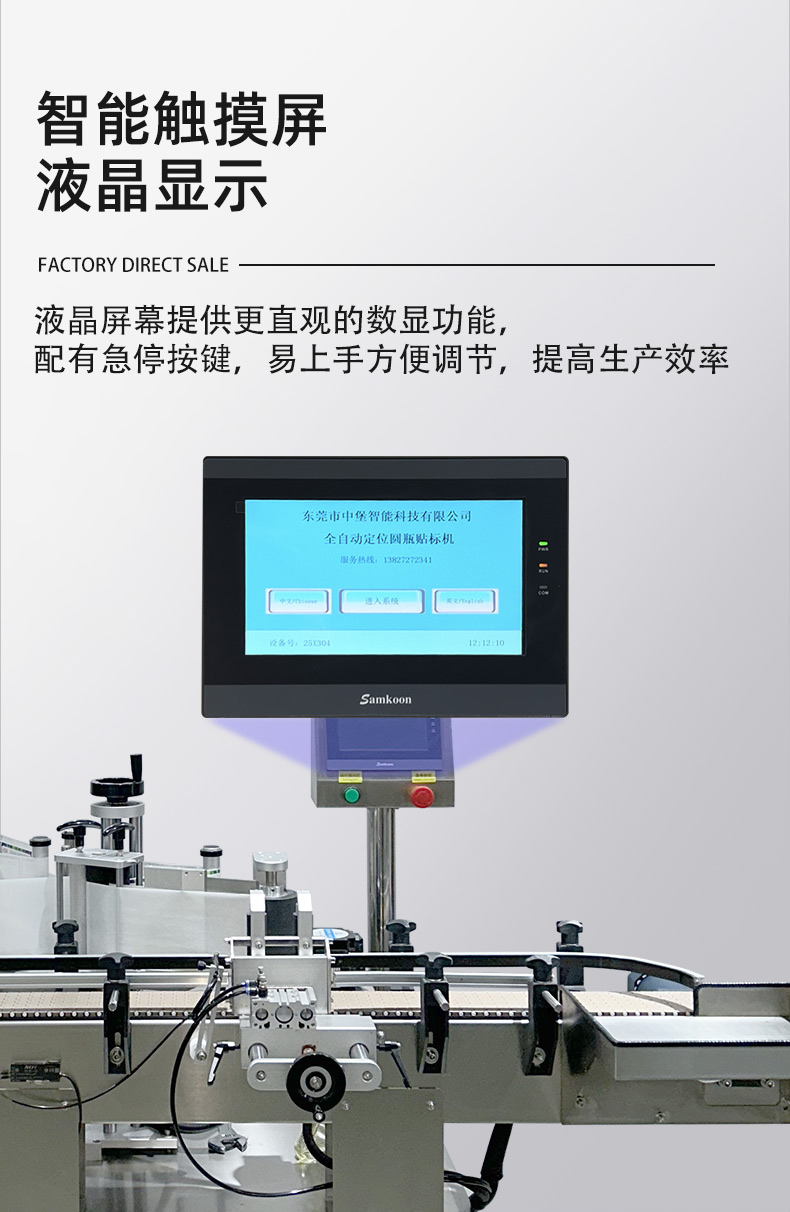

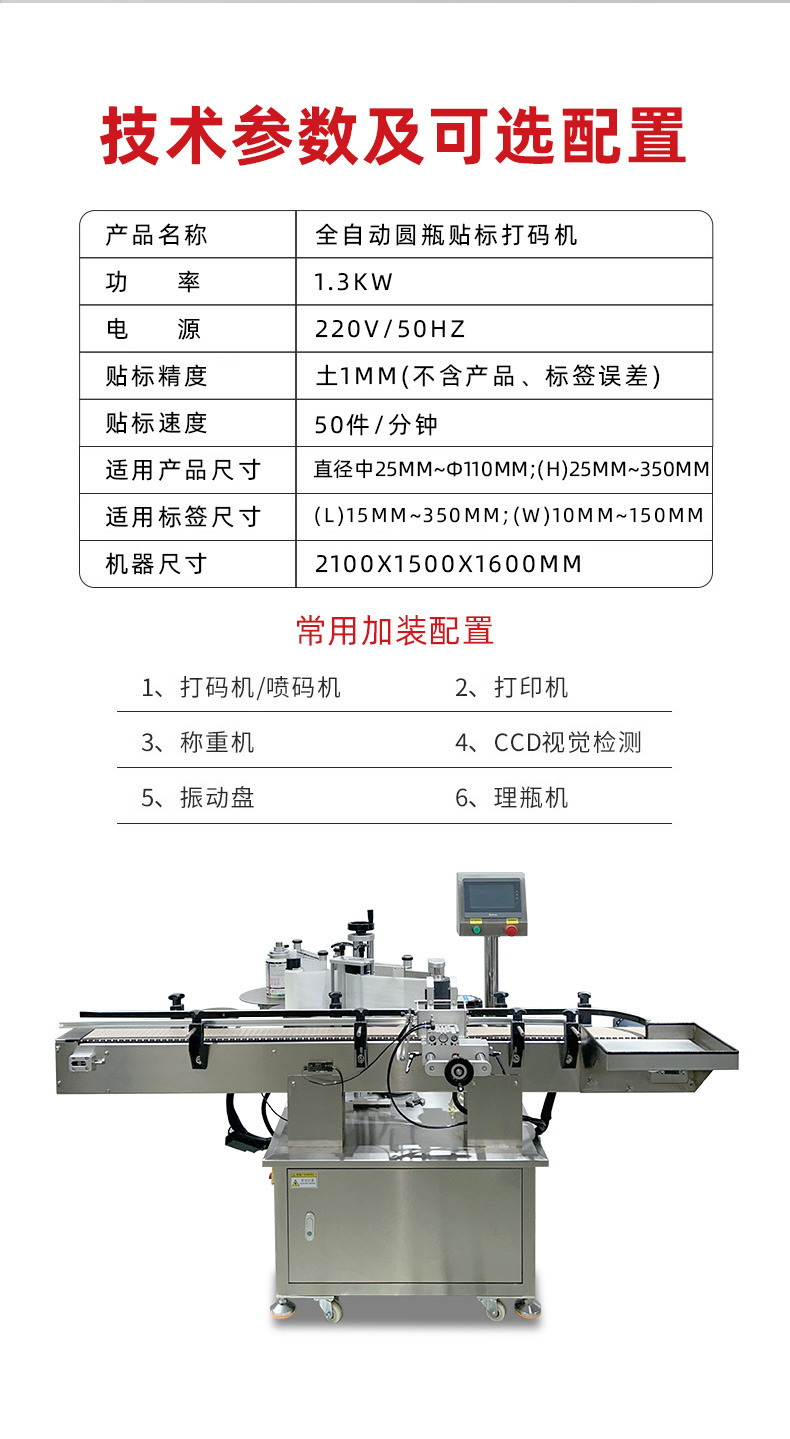

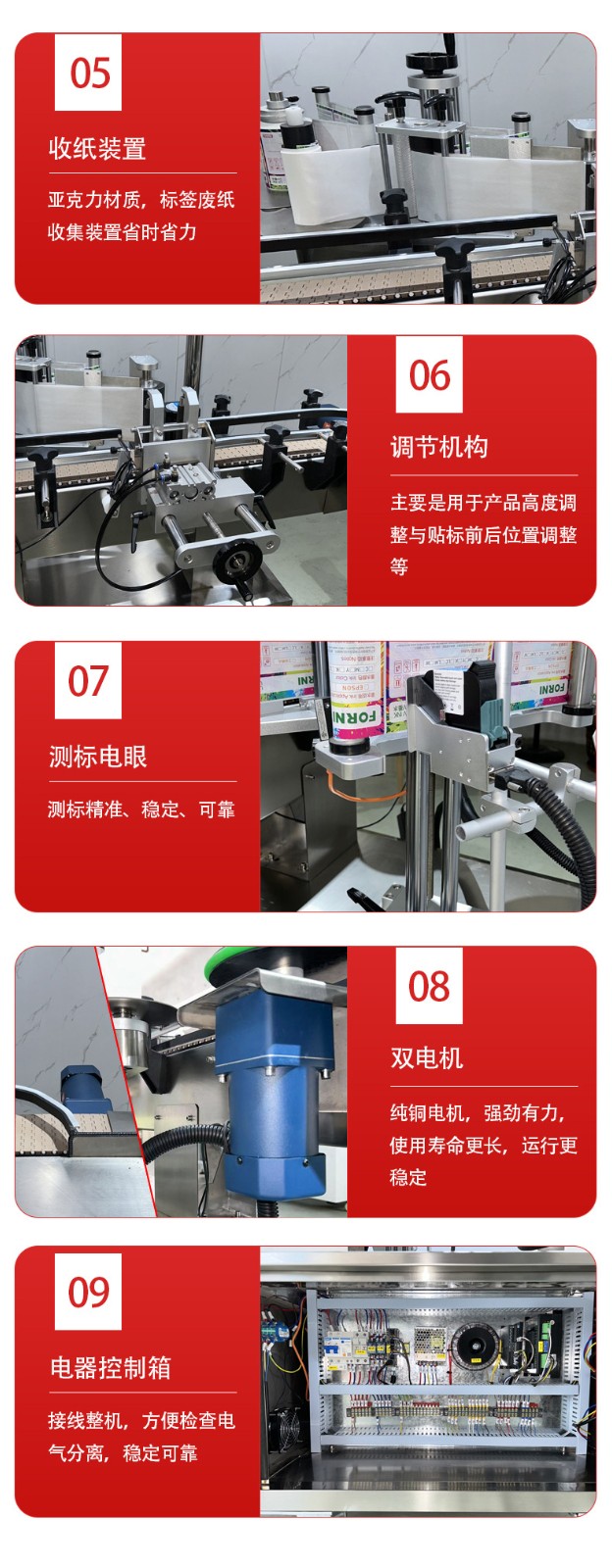
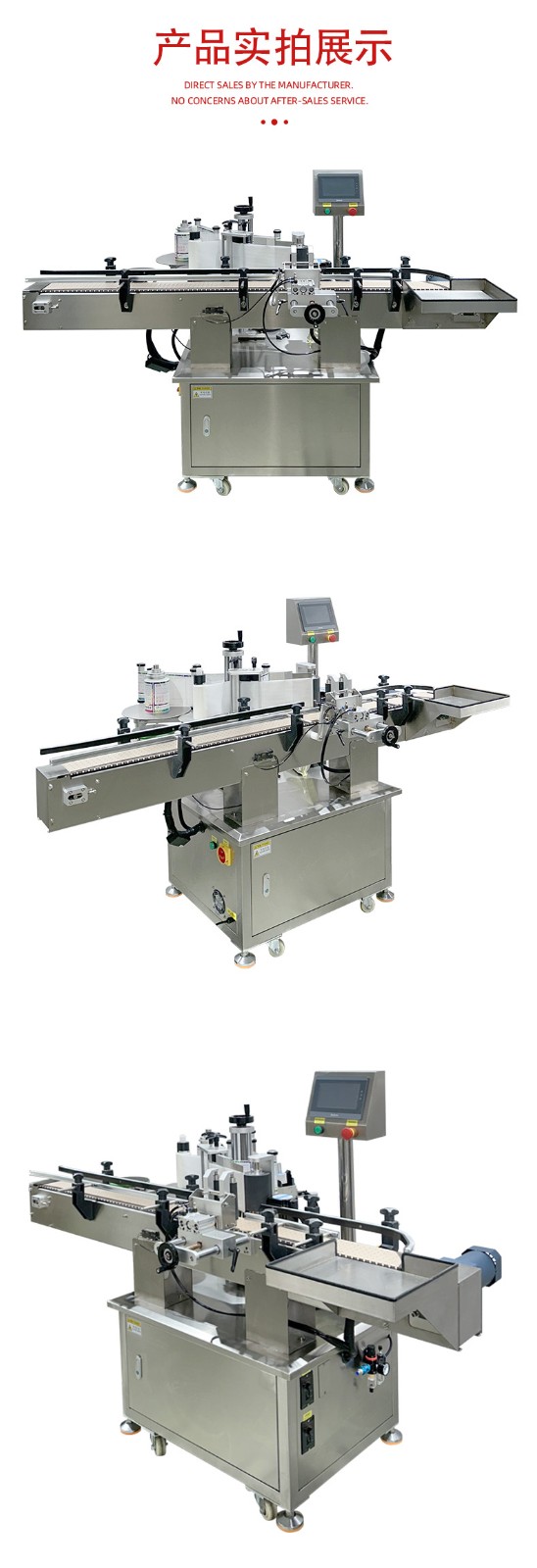