In the traditional packaging process, sealing and corner cutting are often two separate processes that need to be completed on different devices. The transfer of products between processes and the adjustment of equipment consume a great deal of time and labor costs. However, the sealing and corner cutting integrated machine combines these two processes. Through a series of technical means and design concepts, it achieves the automation and continuous operation of the packaging process, significantly improving work efficiency from multiple dimensions.
The sealing and corner cutting integrated machine is equipped with an advanced intelligent control system, which takes an industrial computer or Programmable Logic Controller (PLC) as the core and is complemented by powerful control software. Operators only need to input parameters such as the size, shape, and packaging material type of the product on the human-machine interface, and the system can automatically generate corresponding work instructions. For example, in the food packaging scenario, after inputting the length, width, and height data of a cookie box into the system, the device will automatically set the heat-sealing temperature, pressure, as well as the angle and position of corner cutting. There is no need for manual repeated measurement and debugging, avoiding packaging quality problems and rework caused by human operation errors, and greatly saving time.
The device is equipped with automated feeding and receiving devices, which can be seamlessly integrated with the production line. In the feeding process, devices such as conveyor belts and robotic arms can accurately transport the products to be packaged to the working area of the device at a set pace. After the sealing and corner cutting operations are completed, the receiving device will promptly collect and sort the finished products and transport them to the next process or the finished product storage area. Taking the packaging of electronic products as an example, the robotic arm can quickly grasp mobile phone boxes, complete the processes of film wrapping, sealing, and corner cutting in sequence, and then neatly stack the packaged mobile phone boxes on the conveyor belt. The entire process does not require manual handling, reducing the time consumption of manual operations and also lowering the risk of product damage caused by manual handling.
The sealing and corner cutting integrated machine adopts an integrated structure design, compactly integrating the working modules for sealing and corner cutting within the same device framework. From the moment the product enters the device, it goes through processes such as film wrapping, heat sealing, cooling and shaping, and corner cutting in sequence, and the entire process is completed continuously within the device. There is no need to transfer the product between different devices as in the traditional process. This integrated design eliminates the waiting time during process transitions, making the production process smoother and more efficient. For example, in the cosmetics packaging production line, it only takes a few seconds for bottle - shaped products to be beautifully packaged from the moment they enter the integrated machine, with a compact production rhythm, which greatly increases the output per unit of time.
To meet the packaging requirements of products of different specifications, the design of the sealing and corner cutting integrated machine fully considers the convenience of parameter switching and mold replacement. For parameter adjustment, the device supports the quick storage and retrieval of multiple preset schemes. When it is necessary to change the product packaging specifications, operators only need to select the corresponding preset parameters in the system, and the device can automatically adjust parameters such as the heat-sealing temperature and cutter position in a short time. In terms of mold replacement, a modular and quick-release design is adopted. For example, the cutter mold can be quickly disassembled and installed through simple snap fasteners or bolts, and the replacement process only takes a few minutes. Compared with the traditional equipment, which often requires dozens of minutes for debugging and replacement, it significantly shortens the equipment downtime, ensures the continuity of production, and further improves work efficiency.
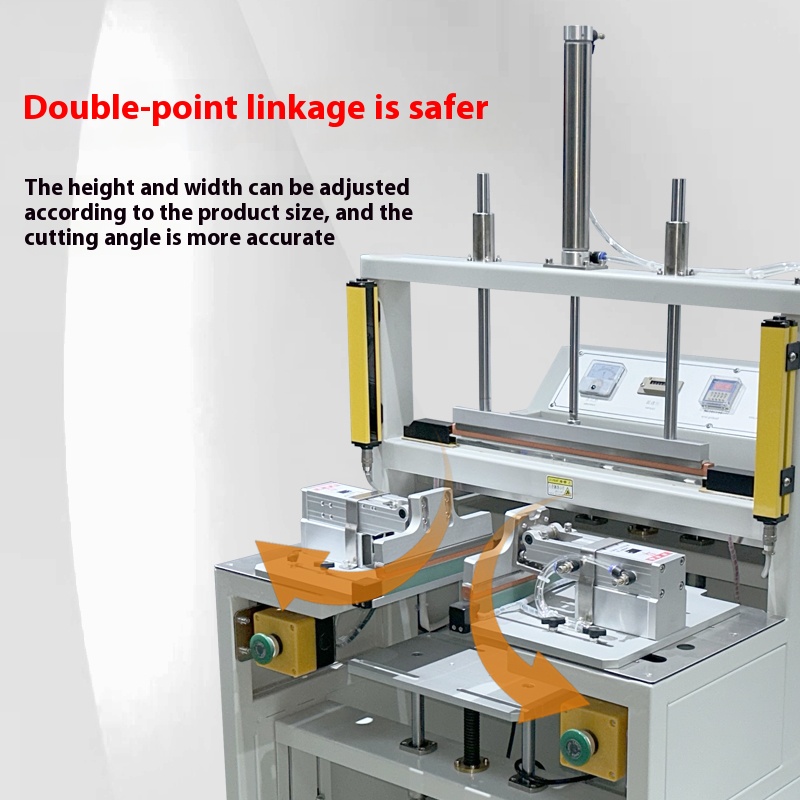

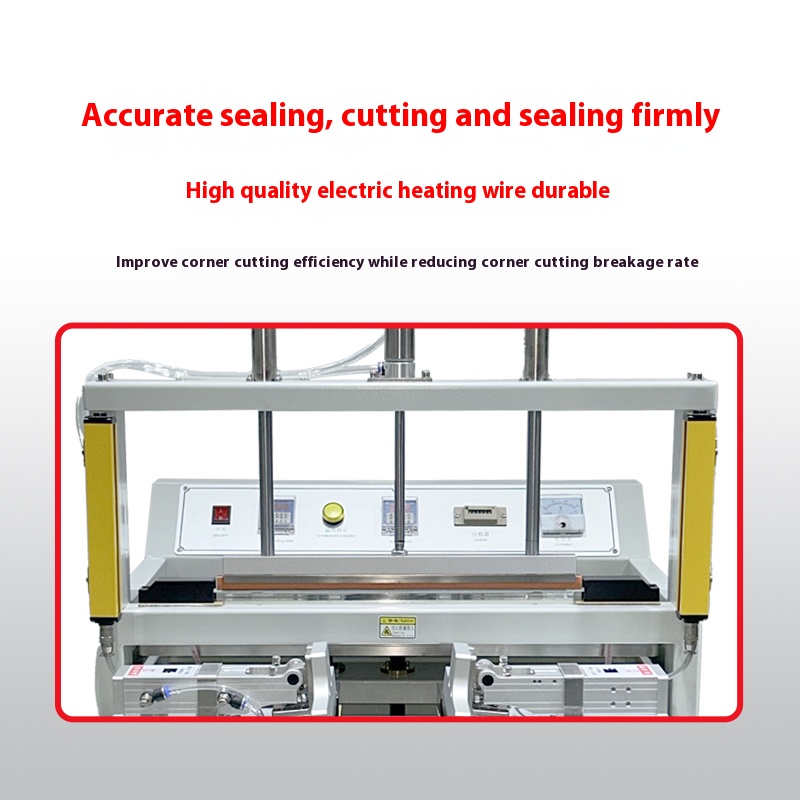
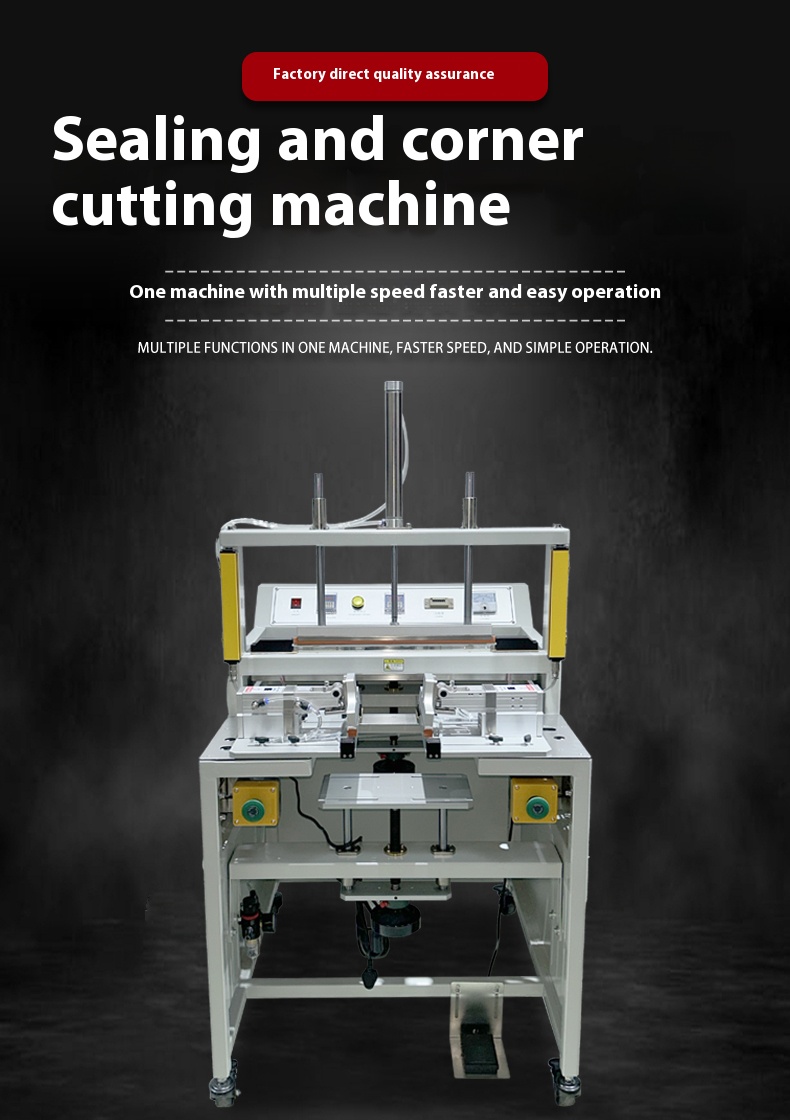
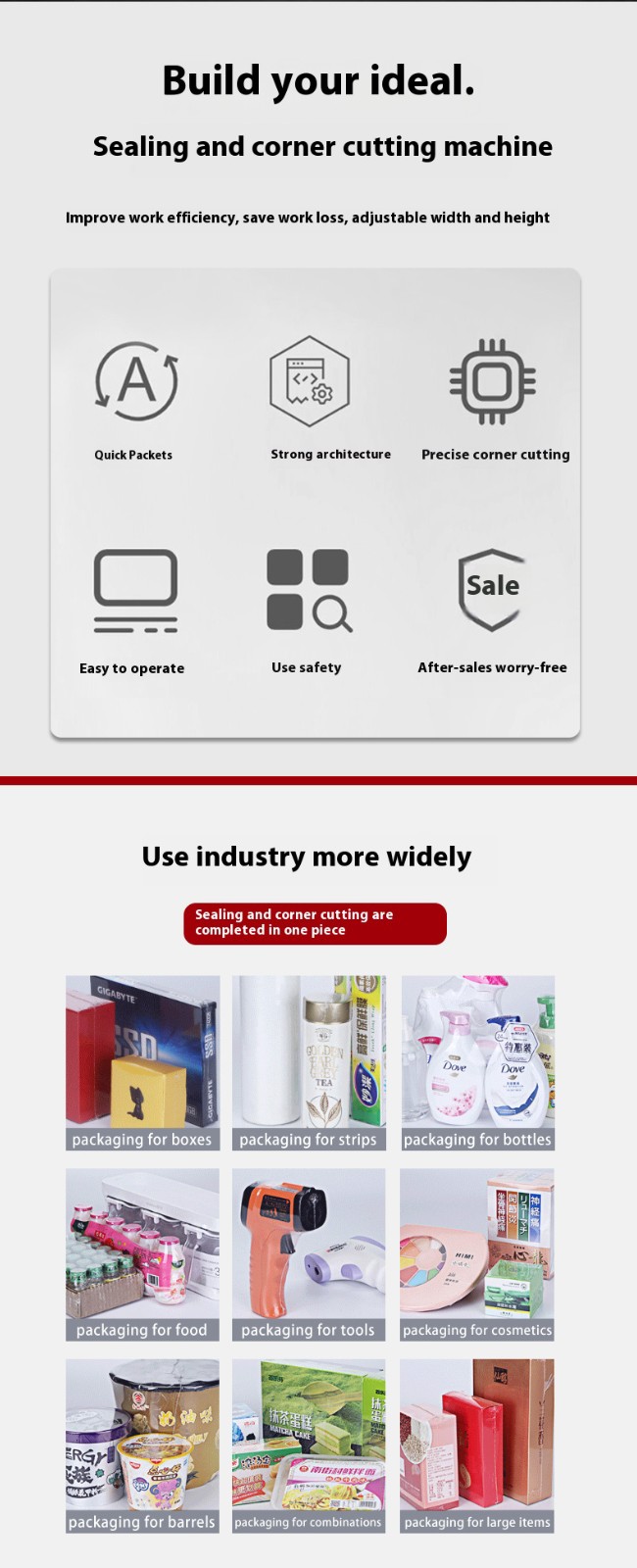
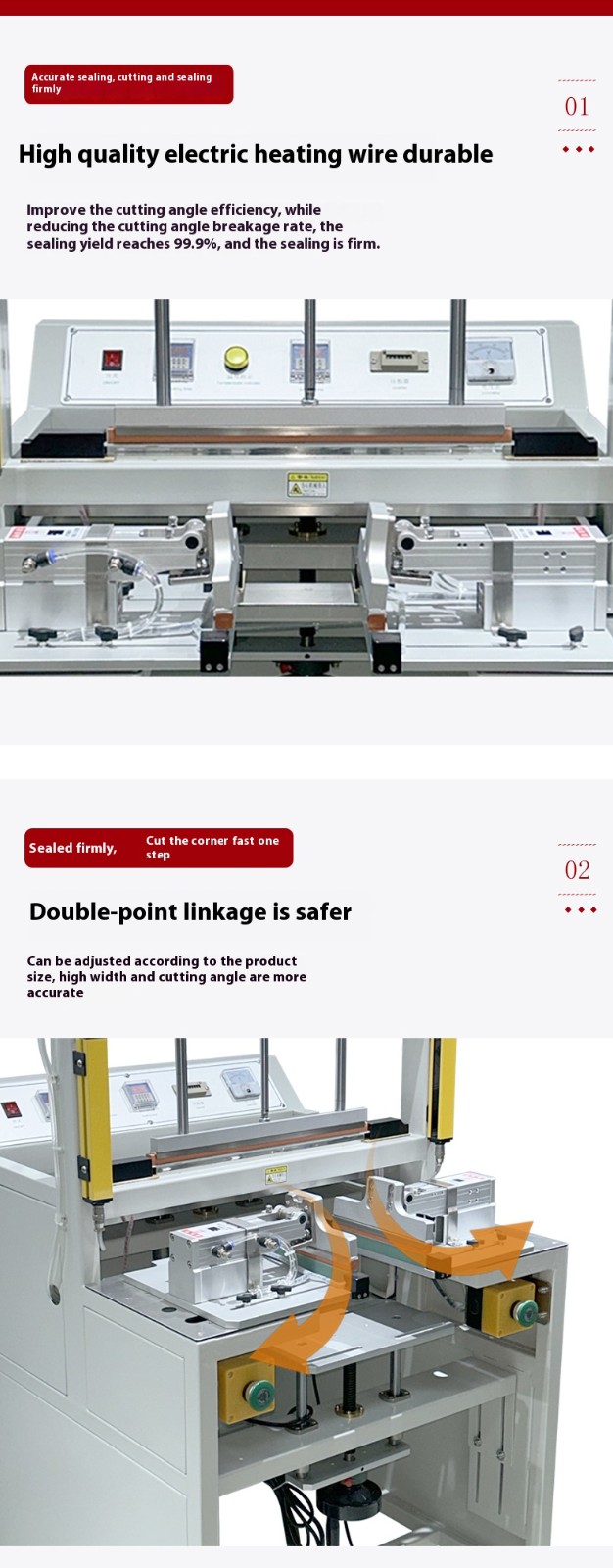
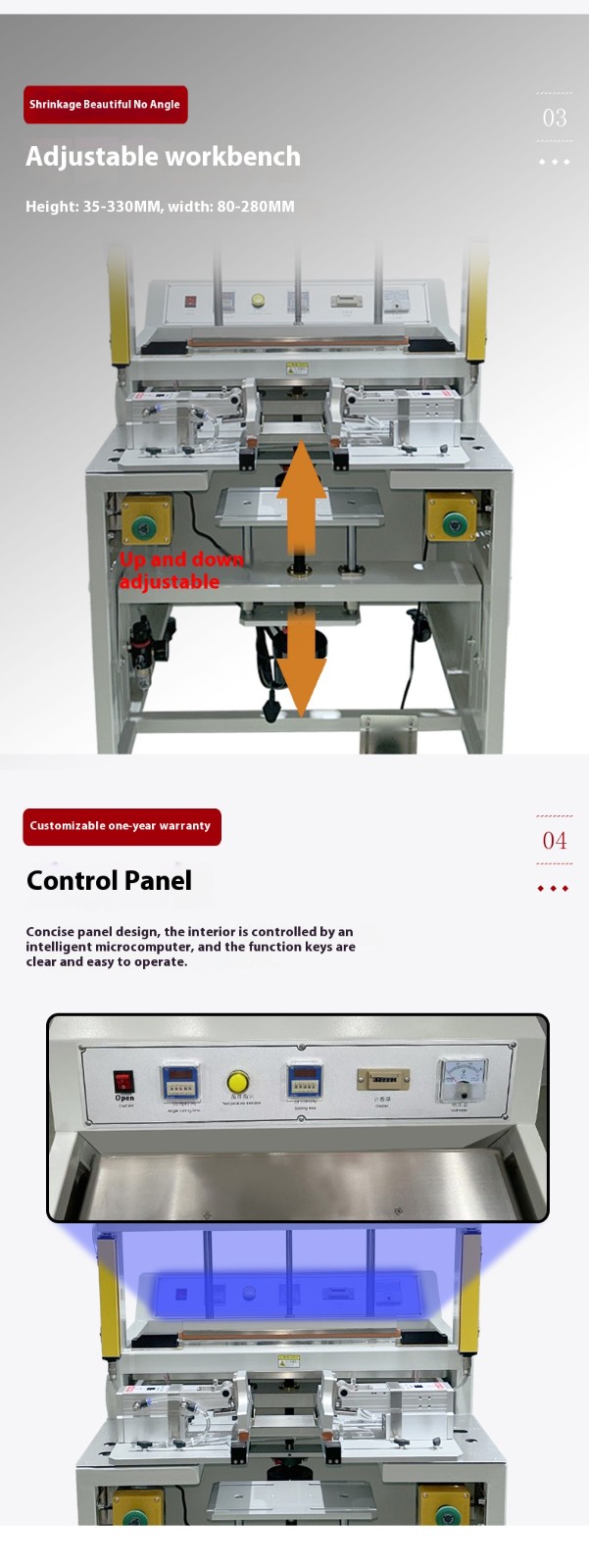
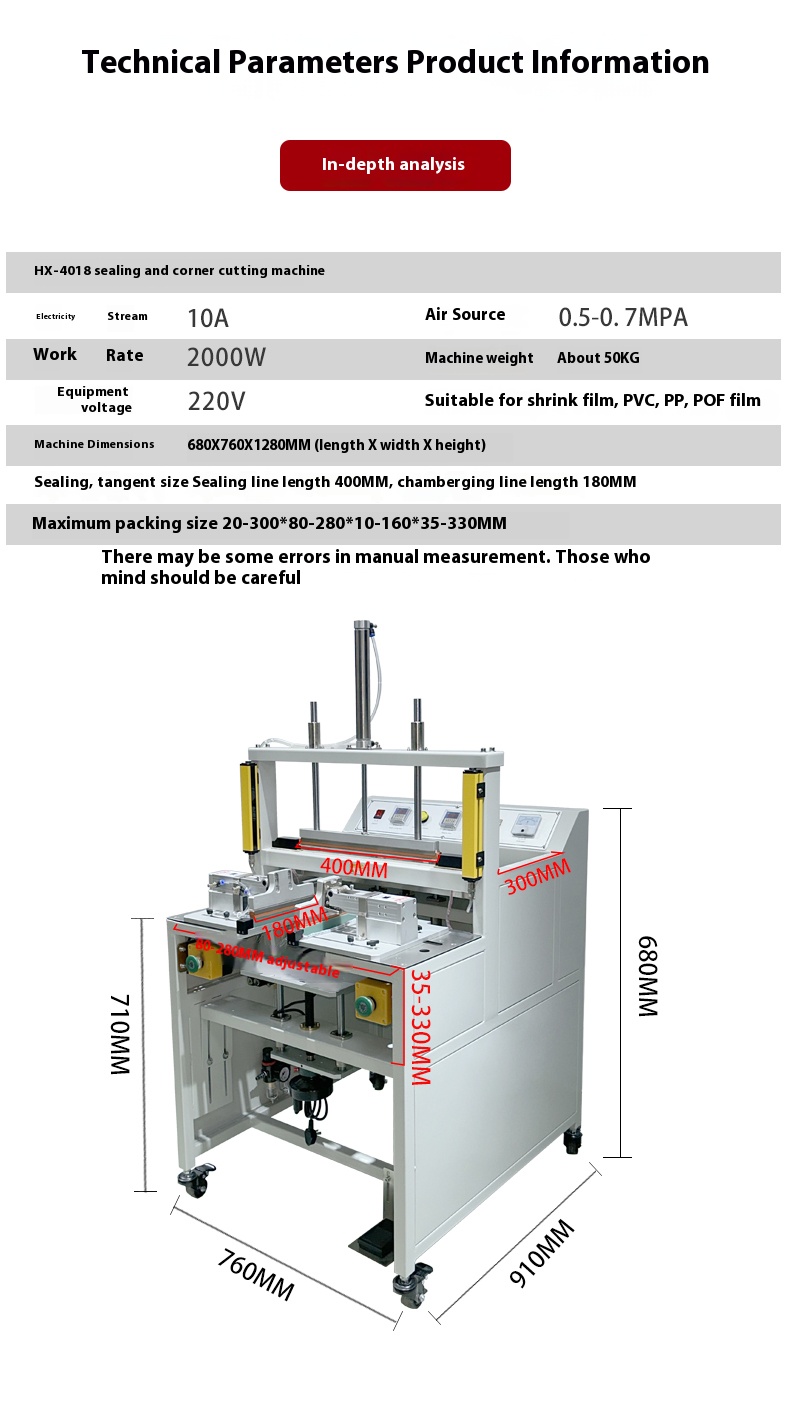
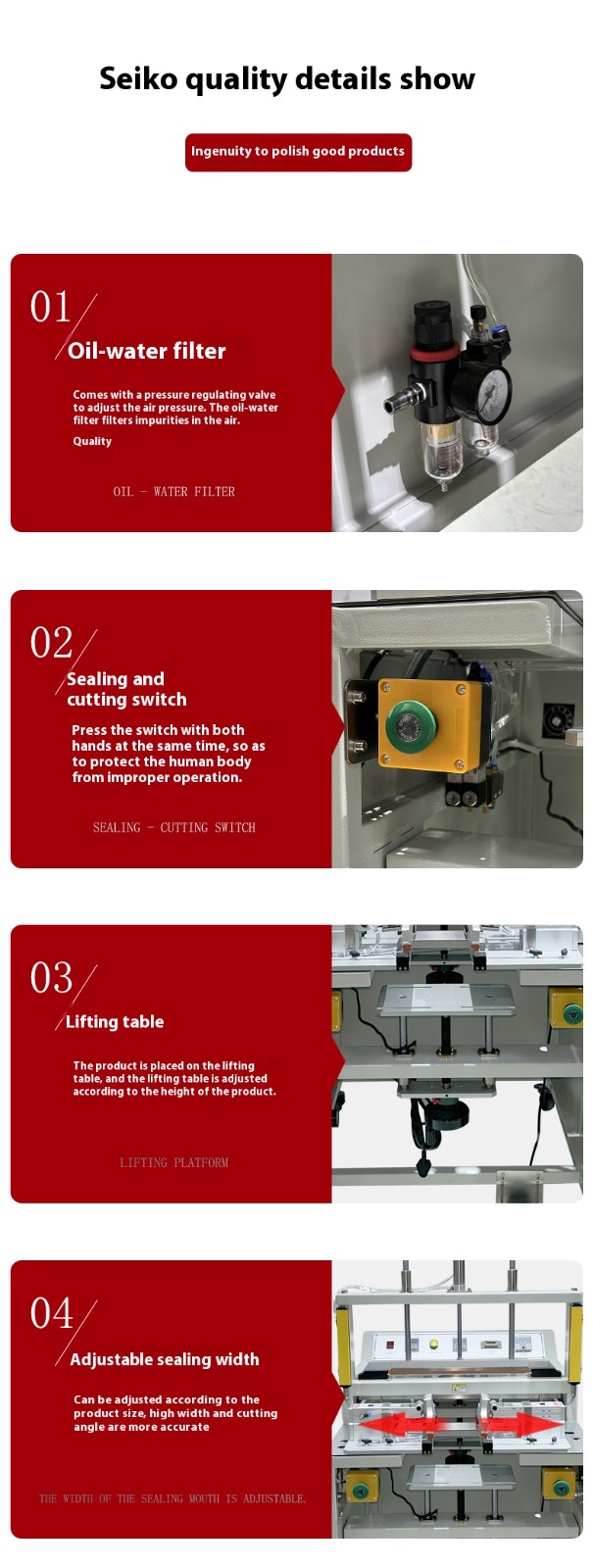

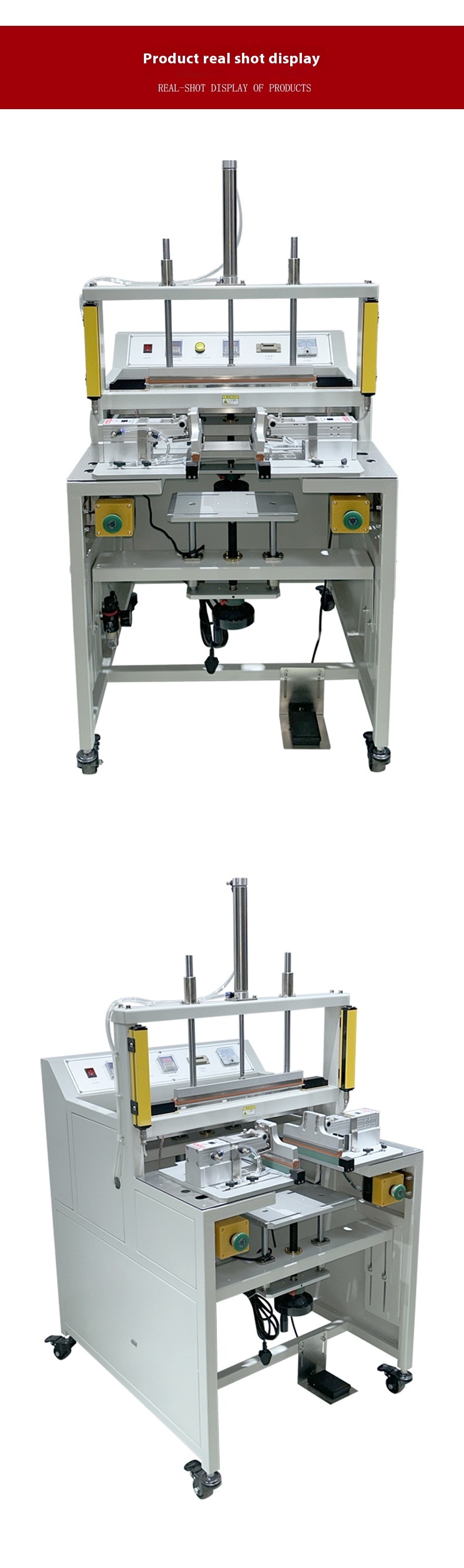